Hans Lapidary Tool
760mmx25mm 600Grit Flexible Diamond Sanding Belts
760mmx25mm 600Grit Flexible Diamond Sanding Belts
无法加载取货服务可用情况
Flexible Diamond Abrasive Belts: Advanced Technical and Operational Insights
Flexible Diamond Abrasive Belts are precision-engineered tools designed for high-performance grinding, polishing, and material removal. Combining cutting-edge materials science with advanced manufacturing techniques, these belts deliver unmatched durability, efficiency, and consistency across industrial applications.
Core Construction & Material Science
Nickel-Plated Binder:
-
A precision electroplating process bonds diamond particles to the belt substrate using nickel. This creates a robust, wear-resistant matrix that prevents diamond loss even under extreme stress.
-
The nickel binder ensures uniform diamond distribution, optimizing cutting efficiency and surface finish consistency.
Diamond Abrasive Layer:
-
Composed of high-purity synthetic diamonds (monocrystalline or polycrystalline), selected for hardness (10,000 HV) and fracture toughness.
-
Grit sizes range from #60 (coarse) to #3000 (ultra-fine), enabling tailored solutions for aggressive stock removal or mirror-finish polishing.
Multi-Layer Backing System:
-
Stainless Steel Double-Layer Backing:
-
Inner Layer: High-tensile stainless steel provides flexibility and fatigue resistance, allowing the belt to conform to complex contours without cracking.
-
Outer Layer: Corrosion-resistant coating ensures durability in wet, dry, or chemically harsh environments (e.g., coolant-assisted grinding).
-
-
Flexible Metal Substrate: A phosphor bronze or specialty alloy base balances rigidity and pliability, maintaining dimensional stability at high speeds (up to 3,000 SFPM).
Ring-Shaped Design:
-
The backing and substrate are laser-welded into a seamless loop, eliminating weak joints and ensuring vibration-free operation.
-
The super-hard diamond coating is applied via electroplating or CVD (Chemical Vapor Deposition), forming a continuous abrasive surface.
Performance Advantages
-
Rapid Chip Removal & Minimal Chipping:
-
Open-coat diamond grit geometry reduces heat buildup and prevents workpiece loading, enabling 20–30% faster material removal vs. conventional abrasives.
-
Ideal for brittle materials (e.g., glass, advanced ceramics) where edge integrity is critical.
-
-
Exceptional Lifespan:
-
1,000x longer service life compared to aluminum oxide or silicon carbide abrasives, reducing downtime and consumable costs.
-
Maintains consistent cutting performance due to diamond’s wear resistance and the nickel binder’s adhesion strength.
-
-
Versatility Across Environments:
-
Performs equally in wet or dry conditions—coolant compatibility prevents thermal damage to heat-sensitive substrates (e.g., aerospace alloys).
-
-
Precision & Consistency:
-
Delivers uniform surface finishes (Ra < 0.1 µm) for applications requiring tight tolerances, such as optical lens polishing or turbine blade finishing.
-
Industry-Specific Applications
-
Aerospace:
-
Finishing carbon fiber composites, titanium alloys, and nickel superalloys (e.g., Inconel) with minimal fiber pull-out or micro-cracking.
-
Deburring complex geometries in jet engine components.
-
-
Ceramics & Glass:
-
Edge-profiling smartphone/tablet glass (2.5D/3D edges) and polishing optical lenses.
-
Precision grinding of technical ceramics (Al₂O₃, SiC) for medical devices.
-
-
Stone & Construction:
-
Lapidary:
Customization & Compatibility
-
Standard Sizes:
-
Widths: 10mm (narrow profiling) to 200mm (wide-surface grinding).
-
Lengths: 500mm–3000mm, compatible with hand-held tools, stationary machines, or robotic arms.
-
-
Tailored Configurations:
-
Cross Belts: Optimized for large-surface grinding (e.g., stone slabs).
-
Fit-to-Hand Designs: Ergonomically shaped for manual grinders to reduce operator fatigue.
-
High-Speed Robotic Belts: Precision-balanced for automated systems (up to 3,000 SFPM).
-
Economic & Operational Benefits
-
Cost Efficiency:
-
70% reduction in consumable costs due to extended lifespan and reduced belt changes.
-
Lower cost-per-part in high-volume production.
-
-
Productivity Gains:
-
Continuous operation minimizes downtime for belt adjustments or replacements.
-
Consistent performance reduces scrap rates and rework.
-
-
Sustainability:
-
Longevity reduces waste generation, supporting eco-friendly manufacturing practices.
-
Why Choose Flexible Diamond Abrasive Belts?
By merging high-grade diamonds, nickel-plated adhesion, and stainless steel durability, these belts redefine abrasive technology. They are the optimal solution for industries demanding precision, efficiency, and cost savings—whether in manual operations, high-speed robotics, or extreme industrial environments.
Grind Smarter. Last Longer. Achieve Excellence.
Share
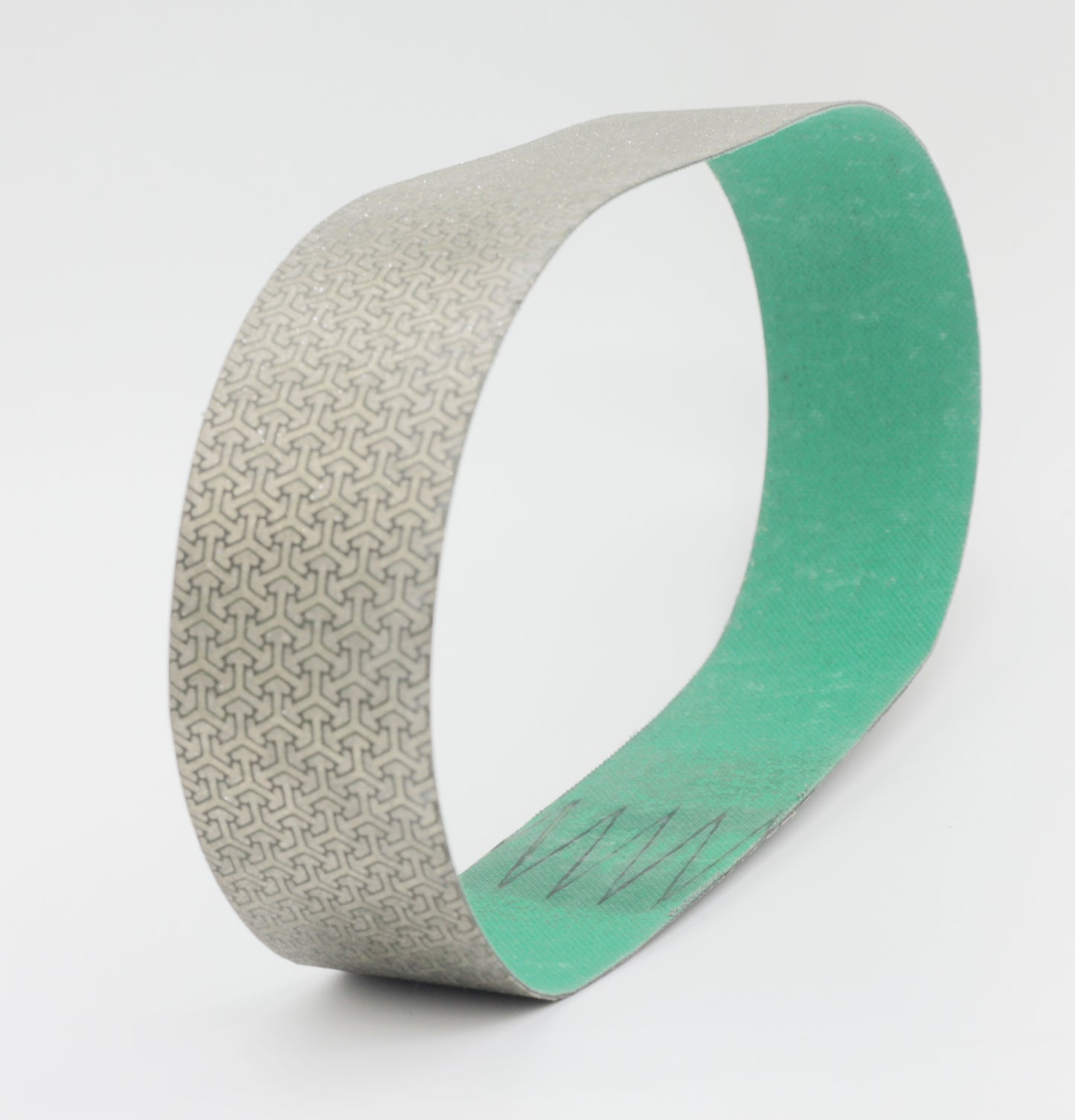
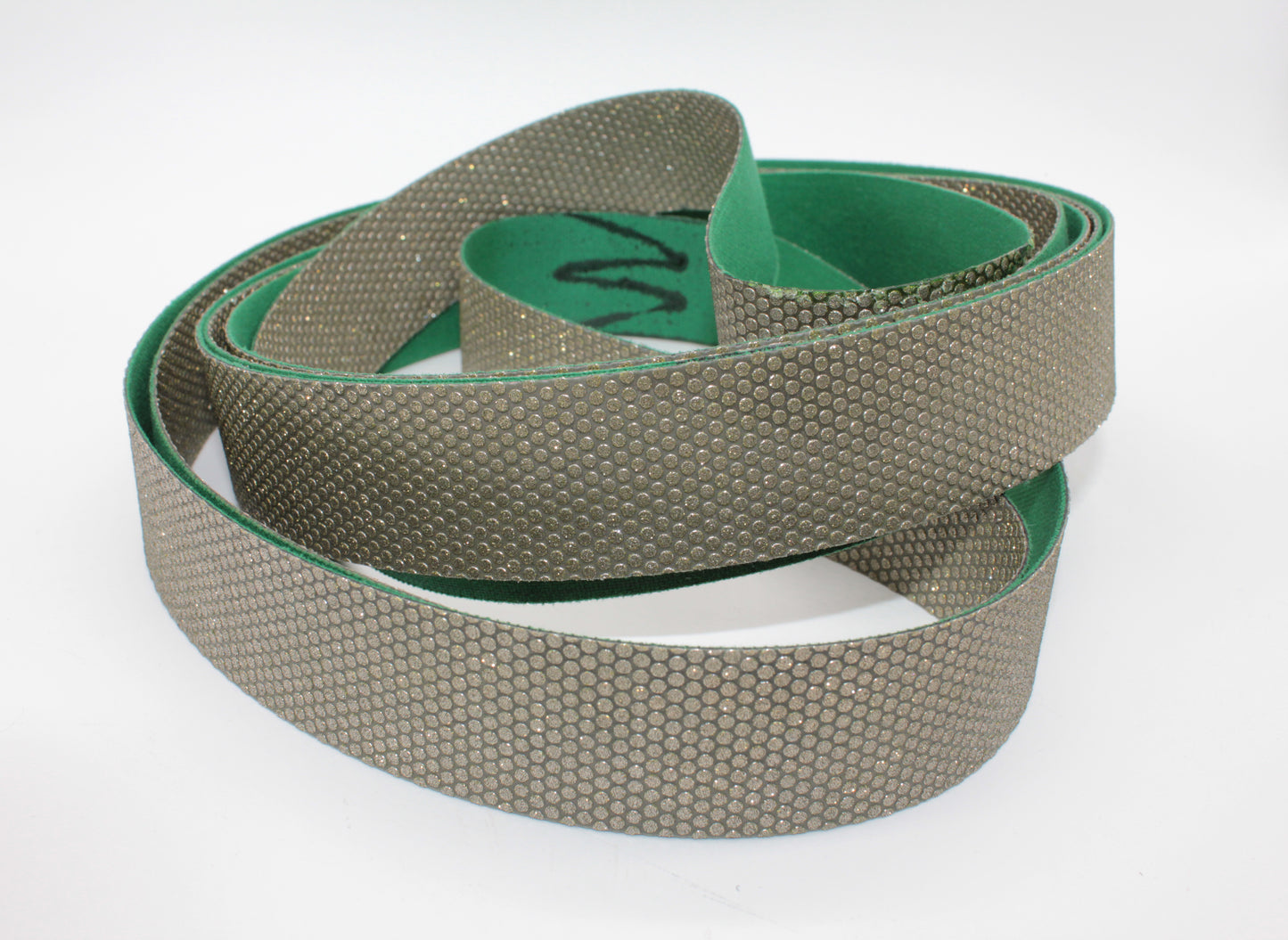